The medical device industry demands extraordinary precision – not just in component dimensions and performance, but in the manufacturing environment itself. As devices become more sophisticated and miniaturized, controlling particulate contamination becomes increasingly critical. This is why HALCO has invested in a new ISO 7 cleanroom facility specifically designed for medical component converting and assembly.
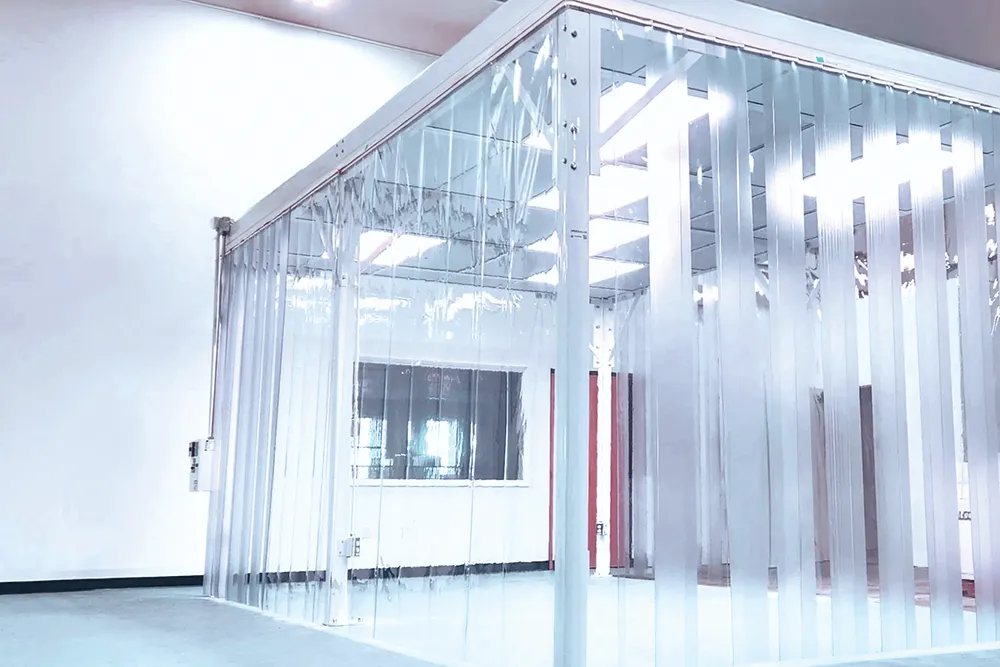
Applications Requiring Cleanroom Converting
While medical devices are the primary application, several industries benefit from cleanroom component manufacturing:
Understanding Cleanroom Classifications and Requirements
Cleanroom classifications are defined by ISO 14644-1, which specifies the maximum number of particles permitted per cubic meter of air. An ISO 7 (Class 10,000) environment allows:
- No more than 352,000 particles ≥ 0.5μm per cubic meter
- No more than 83,200 particles ≥ 1.0μm per cubic meter
- No more than 2,930 particles ≥ 5.0μm per cubic meter
These strict parameters are achieved through:
- HEPA filtration removing 99.97% of particles ≥ 0.3μm
- Positive air pressure preventing outside contamination
- Multiple air changes per hour ensuring continuous purification
- Strict gowning and material transfer protocols
Critical Considerations for Medical Component Manufacturing
When converting adhesives and hook & loop materials in cleanroom environments, several factors become crucial:
Material Selection
- Low-particulating materials that meet USP Class VI or ISO 10993 requirements
- Non-shedding adhesive systems designed for medical applications
- Specialty backing materials compatible with sterilization methods
Process Controls
- Validated cleaning procedures for tools and equipment
- Continuous environmental monitoring
- Regular particle counting and microbial testing
- Documented material flow and handling procedures
Quality Documentation
- Batch records tracking environmental conditions
- Material certifications and lot traceability
- Process validation data
- Personnel training records
HALCO’s Enhanced Capabilities
Our new ISO 7 cleanroom enables precision converting of:
- Medical grade pressure-sensitive adhesives
- Biocompatible hook & loop fasteners
- Clean-compatible interface materials
- Custom die-cut components for device assembly
Through careful specification of materials, precise process controls, and rigorous documentation, we ensure components meet the exacting standards required for medical applications.
The Future of Precision Manufacturing
As medical devices continue to evolve, the demand for ultra-clean manufacturing environments will only increase. HALCO’s investment in ISO 7 capabilities positions us to support next-generation devices requiring pristine assembly conditions.
To learn more about how cleanroom converting can enhance your medical device manufacturing, contact our technical team for a consultation or you can request a free sample of our medical grade fastening materials.
Request a Sample of Our Medical Grade Materials
Tell us a little about your project and specific materials you might want to test.